工場のデータ活用からDXへ 名張ホールディングスの「失敗できるDX」
DX事例 製造業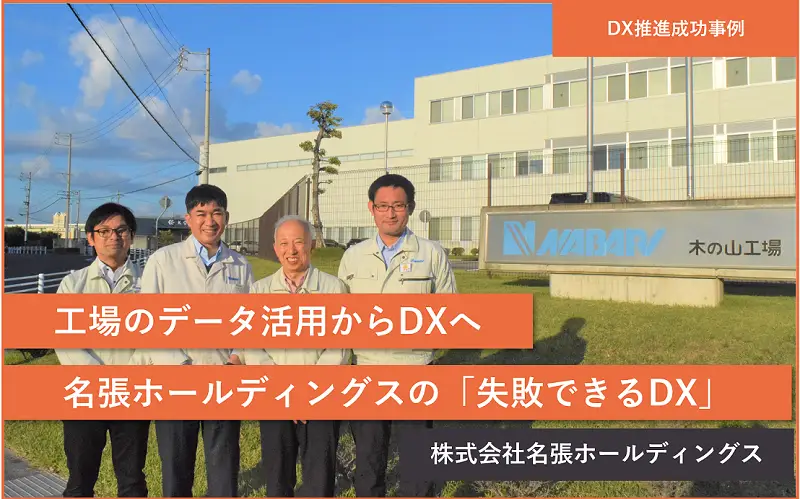
名張ホールディングスは愛知県大府市に拠点を置き、グループ会社の名張製作所ではカーエアコンプレッサー(車両のエアコンシステムで使われる、気体を圧縮して圧力を高める装置)の組み立てや部品加工を行っています。
製造業を本業とする名張製作所では、工場内の様々なデータ活用を通して、エッジデバイスを開発。同社の持ち株会社である名張ホールディングスが、社外のパートナー企業とも連携し、デバイスを外販するまでに至っています。
なぜ本業ではないデジタルの分野で新規事業を立ち上げることができたのか、また、新規事業の立ち上げによって社内でどのような変化があったのか、同社のDX推進に関わる皆さんに語っていただきました。
きっかけは“危機感” デジタルの分野で新しいことを
―― DX推進のきっかけを教えてください。
名張ホールディングス 常務取締役 中村廣一郎様(以下、中村):ひとことで言うと、危機感です。
現代社会は変化が著しく、世界的に脱炭素の機運が高まっていますし、ITが様々な産業を駆逐しています。当社はカーエアコンプレッサーの加工・組み立てをメインで行っているのですが、工場のIT化も進み、部品づくりもどんどん変わっていきます。さらに人手不足の問題もあります。
そのような危機感を抱いたうえで、ひとつの産業に依存していてはダメだという思いもありました。そこで、ビジネスモデルの見直しを始めたのです。新たに事業を考えるとすれば、成長分野であるデジタルの分野がいいと思いました。また、社内でデジタル化を進めれば人手不足も解消できます。
当社は、事業の多角化、デジタル活用、デジタルリテラシー向上の3つの観点から、デジタル製造業を目指してDXをスタートさせました。
名張ホールディングス 常務取締役 中村廣一郎様
―― 最初はどのような規模でDXを始めたのですか?
中村:最初は本当にスモールスタートでした。企画室というものを作って、そこに尖った人材を集めました。若い社員が多かったと思います。企画室では、「新規事業について自由に考えよう」というテーマで活動していて、そこでは本業にとらわれない実に様々なアイディアが出ました。中には、「カラフルなお墓をつくる」なんていうものもありました(笑)
その中で出た、IoTデバイスを用いたデータ活用というアイディアが、新規事業に結びついたのです。
―― 新規事業として具体的にどのようなものを開発したのですか。
ParaRecolectear:パラレコレクター(名張ホールディングス様提供資料)
名張ホールディングス 事業開発部 部長 武藤英行様(以下、武藤):アプリ搭載型オールインパッケージのエッジデバイスとして「ParaRecolectear(パラレコレクター)」を開発しました。設備の改造不要な後付けのデバイスです。
名張ホールディングス 事業開発部 部長 武藤英行様
当社は、古い設備も多く、そのような古い設備にセンサなどの改良を施すのはコストも時間もかかります。そこで、簡単に後付けができるようなデバイスを開発しました。
これは、現場主体でできるDXをコンセプトにしています。現場には温度や湿度、電流、気圧、振動など様々なデータが存在しますが、それが利用価値のあるものなのか、有効なデータとして使えるのか、一目では分かりません。データが使えるのか分からないと次に進めませんよね。しかし、そもそもデータを集めなければ、データ活用はできません。
「ParaRecolectear(パラレコレクター)」は、初期コストが少なく、現場だけでも手軽に始められます。DIY的に始められるので、データが集まるきっかけになるのです。付属しているセンサ以外にも、市販のセンサも接続できるので、どういうデータを取っていいのか分からなくても、とりあえず色々なデータを集めることができる。現場で気軽にトライ&エラーを繰り返すことができます。これを「失敗できるDX」としています。
―― 実際に自社の工場でデバイスを使用して、設備の保全にデータを活用しているのですね。
開発したデバイスを社内で活用(名張ホールディングス様提供資料)
武藤:事例のひとつとして、工場の設備部品の不具合予兆検知に活用しています。例えば、ある設備の部品Aの経年劣化で、加工精度が悪化しているとします。品質不良が発生するとラインを停止して、特急工事で修繕しなくてはなりません。また、製品をサンプリングして測定するのでは、発見するまでNG品を生産し続けてしまいます。
そこで、部品Aの状態をデータ化して不具合の予兆を検知し、品質不良が発生する前に対処できるようにしました。
まずは、部品Aにデバイスを取り付けて、振動値のデータを取得しました。正常時と品質不良時でデータを比較し、振動値と製品品質が比例することが分かりました。
次に振動値のしきい値を設定しました。振動値がしきい値の警告線を越えれば、設備診断と交換部品を準備します。しきい値異常線を超えると交換工事が必要な状態です。しきい値を設定することで、品質不良が発生する前に部品の交換が可能となりました。
このような不具合予兆の検知は、コストというかたちで目に見えて効果が出ます。
部品Aが故障した後の事後保全を行うとすると、設備の修繕工事を外注しなくてはなりません。これが予知保全できると、内部での対応が可能となるので、外注費をほぼ削減することが可能なのです。
工場内の設備にデバイスを設置している様子(名張ホールディングス様提供)
取得したデータを確認(名張ホールディングス様提供)
実際に現場で使ってもらい、成功体験を重ねる。ITリテラシー教育の一助にも
―― 失敗を恐れてなかなかDXに挑戦できないという企業も多くあります。「失敗できるDX」というフレーズはどのように生まれたのでしょうか?
中村:当社はコンプレッサーを製造しているグループ会社、名張製作所の企業理念のひとつとして、「失敗しても良い」を掲げています。製造業なので、もちろん不良品を出さないことは前提にあるのですが、失敗を恐れずに挑戦的、創造的なモノづくりをしていきたいという思いが込められています。
失敗を許容する社内風土、というと大層な物言いになってしまうのですが、そういった企業理念が元にあって生まれた「失敗できるDX」なのかもしれません。
―― 実際に自社で失敗したことや、ぶつかった課題はありますか?
名張ホールディングス 執行役員 福田光伸様(以下、福田):開発したデバイスは、現場で試行錯誤して使えないと意味がありません。今回開発したデバイスを実際に自社の工場で取り入れましたが、しきい値を見出すのに、当初の期待に反して1年近くもかかってしまいました。
実際に現場でデバイスを使う社員は、ITリテラシーを持った者ばかりではありません。当然、導入当時は現場の反発もありましたし、現場のデータを見る目を養う必要があります。いわば人材教育です。
最初こそトップダウンの号令でデバイスを使ってもらいましたが、少しずつ成功体験を重ねることによって、現場の理解も深まっていきました。実際に使ってみて、便利さを理解してもらう、体験して学んでいってもらいました。やはり、自分でデータを使ってみないと分からないですから。
名張ホールディングス 執行役員 福田光伸様
武藤:開発の面で課題だったことといえば、やはり専門的なスキルを持った人材がいなかったことです。開発スキルがないところで、どう開発していくかが課題でした。最初は名古屋の大須の電気街に行って、自分たちで基盤を探すところからのスタートでした。開発パートナーを探すところはやはり難しいところですよね。
―― 現在は外部のパートナーと協業してデバイスを開発していますね。どのように他社と連携していったのでしょうか?
福田:最初は、仕事上でお付き合いのあった企業にお願いしていました。次に展示会で興味を持ってくれた企業や、商社からの紹介など、徐々に裾野が広がっていったのです。
今後事業を展開していくにあたって、いかに当社の事業を理解してくれるパートナーを作ることができるかが重要となっています。企業同士お互いに得意な分野を連携できたらいいですよね。当社の価値も上がるし、協業先の価値も上がる。そんなWin-Winの関係が理想です。
武藤:今後は他社との連携をさらに強化したいと思っています。やはり、ただ「データを取って見る」だけだと、お客様の根本的な課題解決にはなりません。他社のシステムやサービスと連携したり、AIを活用したり、更なる活用方法を模索しています。
トップダウンばかりでは進まない。ボトムアップとのバランスが重要
―― これからDXを始めようとする方にアドバイスをお願いします。
中村:上層部が口を出しすぎるとDXはうまく進みません。とくに若い人たちには言い過ぎずに、自主性を尊重することが大事です。権力というのはやはり恐ろしいもので、自分が思っている以上に部下は委縮してしまいます。そういった距離感や言葉使いなどはとくに気を付けるようにしています。
一方で、企業として人を動かすのはトップダウンでしかできません。トップダウンとボトムアップのバランスが重要です。
デジタルを活用して色々なものをデータ化することで、新しいものが見えてくるようになります。
これから先、モノづくりを日本に残せるようにデジタルを活用していきたいです。
工場内の様子(名張ホールディングス様提供)
取材協力
concept『 学んで、知って、実践する 』
DX SQUAREは、デジタルトランスフォーメーションに取り組むみなさんのためのポータルサイトです。みなさんの「学びたい!」「知りたい!」「実践したい!」のために、さまざまな情報を発信しています。
DX SQUARE とは