まずは「デジタルで楽をする」旭鉄工の事例から見る製造業のDX
DX事例 製造業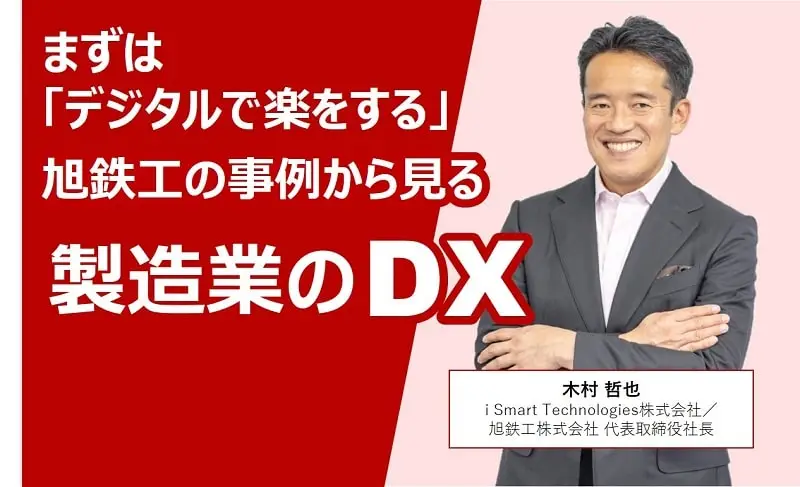
さまざまな業種・企業でDXへの取り組みが活発化しています。しかし、製造業、とくに製造現場ではITの活用が進んでおらず、具体的に何から取り組めばよいのかわからない企業も少なくありません。
IPAでは、製造分野のDXについて、さまざまな事例を公開しています。その事例のひとつとして公開している旭鉄工は、トヨタ自動車の一次サプライヤーである自動車部品メーカーです。IoTやデジタルツールを積極的に活用し生産性を飛躍的に向上させたほか、製造業の枠を超えて、スマートサービスの提供も実現しています。
旭鉄工はどのようにしてDXを実現したのでしょうか。
製造分野DX推進ステップ例(トップと現場によるスマートサービス実現の秘策)から、DXを実現するまでの経緯やきっかけをご紹介します。
本記事は、木村 哲也 氏 (i Smart Technologies株式会社/旭鉄工株式会社)が執筆した「製造分野DX推進ステップ例(トップと現場によるスマートサービス実現の秘策)」の内容をWEB用に再編したものです。
旭鉄工のDXの心構え
旭鉄工は、IoTで生産性向上を実現したメーカーとして知られています。2015年から2018年にかけ、100の製造ラインの平均43%、最も改善効果が高かったラインでは280%(2.8倍)もの生産性向上を実現しています。ここでいう生産性向上とは各製造ライン1時間当たりの生産能力を増やすことをいいます。
この製造ラインの生産性向上は、残業や休日出勤を抑制します。2021年は2015年と比べて労働時間を年間4万時間低減しました。これにより年間4億円以上もの労務費削減に成功、年間31億円の労務費が27億円に減少しました。また、既存の製造ラインをフル活用できることで、設備の増設などの設備投資の抑制にもつながります。
では、その心構えと実際の取り組みを見ていきましょう。
人には付加価値の高い仕事を
旭鉄工の改善活動における合言葉は「人には付加価値の高い仕事を」です。機械やシステムができることは機械やシステムに任せ、人は人にしかできない創造的なことをやるべきだということです。
データの収集は人手でおこなう必要はありませんが、収集したデータから問題を見つけ改善案を考えるのは人にしかできません。であれば、データ収集よりも改善案を考えるほうに人手を掛けるべきです。これが旭鉄工の「人には付加価値の高い仕事を」です。実際に旭鉄工では改善活動に必要なデータを社員が集めていましたが大きな負担となっていました。これを、IoT技術を使って自動でやろうとしたのが出発点です。
DXを難しく考えすぎない
「改善とは人を楽にすること」であり、旭鉄工の改善活動で常に心掛けているのは「人が楽になるかどうか」です。改善活動の結果として人に負担が掛かるようであればそれは改善ではありません。何かの拍子に元に戻りますし改善活動に協力してもらえなくなります。まずは「デジタルで楽をする」ことを考えましょう。
具体的にはスケジューラ・ビジネスチャット・ファイル共有あたりから始めてみてはいかがでしょうか。うまく使うと情報共有の程度・速さが大きくレベルアップするとともにコミュニケーションコストが下がります。旭鉄工の事例として、「社内の危険個所の共有」をご紹介します。
旭鉄工ではSlackというビジネスチャットを使用しています。ある日製造現場の課長から「路面がひび割れていて台車のタイヤがはまって転倒の危険がある」とのコメント付きで写真が投稿されました。すると、わずか3時間後に総務から「直したので確認お願いします。」という写真がアップロードされました。
製造分野DX推進ステップ例(トップと現場によるスマートサービス実現の秘策)図3.4-1より
圧倒的なスピード感と低いコミュニケーションコストです。こうなると、ほかの不具合もどんどんこのチャンネルにアップロードされるようになり、どんどん会社はよくなります。不具合を連絡する書類をデジタル化しよう、という発想ではこうはなりません。書類を作成する概念すらすっ飛ばしたのがこのアイデアなわけです。
このような従来の仕事のやり方にとらわれない効率化に人が慣れると、「デジタルで楽をする」アイデアがどんどん出てくるようになりDXを実現する土壌になります。
旭鉄工の改善活動
ここからは具体的に、年4億円以上の労務費削減効果を出した旭鉄工の改善活動を見ていきましょう。
儲かるIoTデータを収集
まず、問題は数値にして比較し、見える化することが必要です。そしてそれをビジネスへの貢献に繋げる。つまり、見える化した問題に対してアクションを取りビジネスに貢献して初めてツールを生かしたことになります。旭鉄工ではこの「ビジネスへの貢献」が「時間当たりの出来高の向上による労務費の削減」なわけです。
見えた問題を直して、果たしてどれだけ儲かるのか? 効果の金額換算が必要です。旭鉄工では1時間当たりの生産個数を増やすことに集中しています。そのために注目している観点が停止とサイクルタイム(製品が生産される時間間隔)の遅れです。
多くの会社では停止をそもそも記録していません。「弊社では記録している」とおっしゃる経営者の方も多くいらっしゃいますが、正確性に欠ける人手による記録がほとんどです。その場合、短い停止は記録されませんし、記録される時間は人の感覚による大雑把なものです。結果、実態よりも2割程度短く記録されています。経営者には細かいトラブルの停止報告が入らないので「弊社の製造ラインは停止が少ない」といった勘違いに繋がります。
サイクルタイムはほとんどの会社で正確に把握されていません。把握されていたとしても製造ラインを敷設したときに測定したなど古い数値だったりしますし、ましてや作業者の熟練度や疲労度によって1日のなかでも変動するサイクルタイムを把握している会社はまずありません。
製造分野DX推進ステップ例(トップと現場によるスマートサービス実現の秘策)図4.3-1効果の金額換算より
このような短時間の停止は見えないので損失に気がついていないだけなのです。IoTで実際の数値を見るとイメージと大きく違うと実感することでしょう。気づかないうちに損しています。
改善活動を現場以外の業務に組み込む
改善活動は現場がメインです。しかし、会社は、改善活動を活用する仕組みを作ることで現場の改善を早く進ませることができます。それは、改善活動を現場以外の通常業務の一環として組み込むことです。
旭鉄工では毎年の改善目標(労務費を全社で1億円節減など)が各部・各課に割り当てられます。その進捗確認のために収支フォロー会議というものがあります。月次決算をおこなった結果出てきた経理の数値のうち主要15項目についてグラフ上にプロットします。このグラフを使って、予定通り改善効果が出ているかをチェックするのです。そして製造の部課長からは前月の改善内容とその効果の金額換算値、今月の改善計画などが報告されます。経理の数値チェックと現場の改善進捗チェックが同時におこなわれるわけです。
改善のなかには実行しても利益に繋がらないものがあります。経理の数値をチェックすることで「儲からない改善」ではなく経理の数値にキチンと反映される「儲かる改善」がおこなわれるようになります。
また、原価管理にもIoTは活用されています。製品が量産化されるまでの過程の節目節目で原価がチェックされます。収益悪化を見逃さない仕組みと言えるでしょう。このように改善活動と経営状況の繋がりを金額ではっきりさせることでより改善活動がやりがいをもって進められるようになります。
製造分野DX推進ステップ例(トップと現場によるスマートサービス実現の秘策)「図4.6.1-1会議体でのデータ活用」より
現場で改善を回す
現場は全社目標から割り振られた金額目標を達成するための改善活動をおこないます。そこで最も大事な日常の活動が「ラインストップミーティング」です。
現場の作業者から管理監督者や生産技術担当者など必要なメンバーが毎日決まった時間に製造現場に集まります。前日の稼働のデータを用いて問題点や改善効果などを確認し、取るべきアクションと期日を決めます。このミーティングで使うのが「横展ボード」です。このミーティングは毎日おこなうのがポイントです。前日に起こった問題点なら作業者に聞けば詳細を確認できますが、1週間前の問題では正確な情報を聞き出すことはできません。
「データに基づいた現地現物」が必要です。IoTを使えば現地現物が不要になるわけではありません。現地現物の重要性は変わりません。IoTを活用することで現地現物がより強力になる、と考えるほうが適切です。このミーティングでは稼働状況のデータが必要です。人手によるデータ収集では手間が掛かりすぎて困難で、IoTで自動収集されたデータだからこそみんなで現場を確認し、対策を進めることができるのです。
製造分野DX推進ステップ例(トップと現場によるスマートサービス実現の秘策)「図4.6.2-1 現場での改善活動」より
まとめ~製造分野DX推進ステップ例を読んで、スマートサービス実現の秘策も知ろう
ここまでの内容からわかるようにIT部門に丸投げするだけでは、DX推進はできません。
「DXとは変革」ですから、既存のルールや組織と相容れないことがあるのは当然です。「競争上の優位を確立する」ために背反や問題を解決、もしくは一定程度許容しつつ邁進することが必要です。
旭鉄工では経営者が先頭に立って、積極的なデジタル活用をおこなっています。それによって生産性の向上を実現したばかりでなく、デジタル活用をブラッシュアップし続けることで、「ノウハウ」という財産を得ました。
そして、本業である製造業の枠を超えて、IoTサービス提供とコンサルティングを手掛ける会社を設立するまでに至ったのです。製造現場の係長だった人がコンサルタントとしてお客様の稼働データを分析し改善点を洗い出し、改善指導をウェブサイトでおこなっています。
自社の生産性向上のノウハウを「スマートサービス」として他社展開する旭鉄工。その実現についての全文は以下の資料でご覧いただけます。
製造分野DX推進ステップ例(トップと現場によるスマートサービス実現の秘策)
DX推進のためには、まずは挑戦してみることが大切です。他社の事例を参考にして、身近なところから取り組みを始めてみてはいかがでしょうか。
concept『 学んで、知って、実践する 』
DX SQUAREは、デジタルトランスフォーメーションに取り組むみなさんのためのポータルサイトです。みなさんの「学びたい!」「知りたい!」「実践したい!」のために、さまざまな情報を発信しています。
DX SQUARE とは